Kaizen Event Overview
“Kaizen” is a compound Japanese word. “Kai” means little, ongoing, and good, and “Zen” means for the better. Kaizen grows out of the famous Toyota Production System where the focus in on engaging employees in ongoing, small, continuous improvements.
Kaizen events are designed to be short term (3 to 5 days), highly engaging (eight to ten employees devoted full time to the process for the 3 to 5 days) events that focus on improving one to a few targeted areas. Kaizen is an example of change at the micro level; as opposed to large scale change efforts such as Six-Sigma or Process Re-engineering efforts.
The 11 Wastes
Kaizen events focus on eliminating waste and thereby dramatically improving processes, productivity, and effectiveness. The “eleven wastes” identified by Dr. W. Edwards Deming and his associates can all be included in Kaizen events. These eleven wastes include:
- Complexity
- Errors in documents
- Transport of documents
- Underutilized staff & overstaffing
- Process of getting approvals — unnecessary reviews and signatures
- Lack of standardized processes
- Backlog in work queues
- Unnecessary motions
- Unnecessary amount of supplies
- Waste of staff time – waiting for instruction, material, data, information, unnecessary meetings, unnecessary travel
- Unnecessary reporting and reports
Value Stream Mapping
A Kaizen event usually includes a Value Stream Mapping (VSM) exercise. VSM is a process that highlights potential areas for improvement. The Value Stream Mapping (VSM) Session will consist of describing each step in a process from Customer Demand to Supplier Delivery. A weighted priority matrix is developed to rate each potential area on ease of implementation and potential impact to the business. The process concludes with a prioritized list of areas for potential Kaizen Projects.
Event Schedule
The schedule for a typical five day Kaizen event and the activities that precede it and follow it is as follows:
Timeframe | Activity |
Six weeks before the event | Select the process/target area for the event |
Five weeks before the event | Draft the team charter |
Four weeks before the event | Select the Kaizen event team members |
Two weeks before the event | Communication (about the event, expected outcomes, etc…) |
Day One, AM | Kickoff and train team members in Kaizen tools &philosophy |
Day One, PM | Create value stream map of the process |
Day Two, AM | Document the current state/practices using observation, performance metrics, written procedures, customer survey feedback, employee survey feedback. Identify lead time, process time, critical path, and obstacles. |
Day Two, PM | Identify waste and perform root cause analysis |
Day Three, AM | Brainstorm and prioritize improvement options |
Day Three, PM | Brainstorm and prioritize improvement options |
Day Four, AM | Design and test improvements |
Day Four, PM | Design and test improvements |
Day Five, AM | Implement improvements & prepare training materials |
Day Five, PM | Team presentation to management & event wrap up |
One week after the event | Workforce training in improvements |
Thirty days after the event | Review Parking Lot issues and 30-day list issues |
Forty-five days after the event | Review sustainability plan |
Next three quarters | Report to management on impact of event |
Process Improvement Tools
Tools that can be covered during the initial training and during the week (as they are needed) can include:
- Lean enterprise principles
- Value stream mapping
- Six step problem solving process
- S-T-P Problem solving (Situation – Target – Proposal)
- Root cause analysis
- Brainstorming
- Cause and effect diagrams
- Five S housekeeping: sort, straighten, shine, standardize, sustain
- Ask “Why” five times
- Kanban cards/systems to control inventory and supplies
- Check sheets to collect data
- Pareto charts to prioritize data
- PACE charts to prioritize actions (Priority – Action – Consider – Eliminate)
Typical Results
An organization that engages in a Kaizen event can expect to see rapid and dramatic improvements in the targeted work processes. Typical results of Kaizen events include*:
- Faster turnaround
- Improved quality
- Improved productivity
- Reduced costs (due to the elimination of waste)
- Employee engagement
- Enhanced job satisfaction
Many businesses see dramatic results after Kaizen events. For example*, one healthcare organization reduced delays in care from 35% to 15% of their patients, resulting in increased customer loyalty. A manufacturing company reduced the turnaround time to process its sales orders from 7.5 days to just under 2 days, greatly increasing cash flow and customer satisfaction.
*The Kaizen Event Planner by Karen Martin and Mike Osterling
Related Stories
Team Performance , Strengthening Organizations , Coaching
Burnout & Resilience Insights: A Conversation Between Workplace Psychologists (Part 3 of 3)
Team Performance , Strengthening Organizations , Coaching
Burnout & Resilience Insights: A Conversation Between Workplace Psychologists (Part 2 of 3)
Ready to take your organization to the next level?
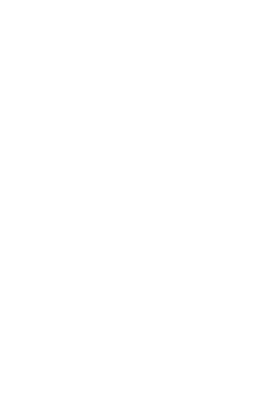