Using Employee Involvement To Drive Employee Engagement
Columbia Aluminum – Located east of Seattle on the Columbia River by the John Day Dam
Background:
The Goldendale, WA aluminum smelter closed after a number of different companies tried to make the plant profitable. The closure put 600 people out of work. Later that year an entrepreneur purchased the plant with a vision of creating a culture of ownership where all employees would be committed to the success of the company.
Former plant employees welcomed the re-opening of the plant. The company was the preferred employer in the area offering year round work and high wages.
The new owners wanted employees and their union to have a better way to get their ideas before plant management. They announced an open door policy. They solicited employee suggestions. They invited employees to share their ideas with their supervisors. They asked union leadership for their help. And nothing significant happened.
Plant management invited the Steelworker’s union president and union council to a meeting to explore ways in which all employees could have a way to use their creativity to contribute to the success of the company. They knew that other companies across America were successfully involving their employee. They just didn’t know how to do this at Columbia Aluminum.
Plant management and union leadership created a labor management committee with two goals:
1. Learn about employee involvement and employee engagement
2. Investigate what other organizations in the United States were doing to create a culture of involvement and engagement.
3. Design an involvement/engagement process that would work at their plant.
The seventeen member labor management committee was divided into four teams that travelled to numerous manufacturing sites across North America. They asked questions, they observed, they took copious notes.
The team members returned to the plant and spent almost two months reviewing what they had seen and deciding which approaches would work at their plant.
Their employee involvement/engagement design was elegant in its simplicity. It included the following components:
- Plant wide steering committee to guide the effort
- Steering committee sponsored task forces that cut across department lines
- Individual supervisors led improvement teams composed of their employees
- Managers and supervisors participated in five days of training
- Problem solving team members participated in twenty hours of training
- Facilitators were selected from the existing workforce
- Facilitators supported all problem solving teams
- Problem solving teams met weekly
- Took most team a dozen meetings to identify solutions
- Solutions presented to the steering committee
The results were startling:
- Over 60% of employees actively engaged on problem solving teams within 24 months after launch
- Labor-management cooperation improved dramatically
- There were many improvements in production methods, safety, waste reduction
- Productivity improved 6% during the first year after rollout
- Return on Investment (ROI) for the costs involved in designing and rolling out the process during the first year was over 1,000%
- Product quality was higher than competitors
The process was a resounding success. To take involvement to the next level the owner of the plant created an ESOP (employee stock ownership plan) so that all employees could share in the gains. Over the next few years the ESOP purchased 100% of the plant.
The high degree of employee involvement resulted in a much higher degree of employee engagement than anyone could have anticipated.
Related Stories
Coaching, Developing Stronger Leaders, Employee Engagement, Leadership Development, Performance Management
Increase Employee Engagement by Training Front-Line Managers to Coach
Ready to take your organization to the next level?
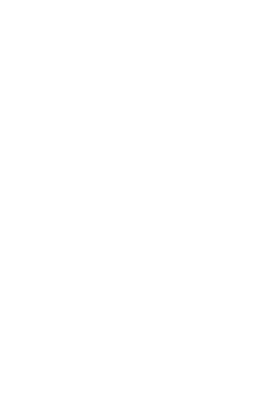